From ancient times to the present, the foundry remains an indispensable cornerstone of production, shaping the world around us with its diverse range of products. In our foundry, we use advanced and efficient processes that ensure the production of high quality castings.
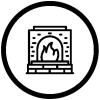
As a melting device we use a pair of EGES electric medium-frequency induction furnaces with a capacity of 2×6 tons. These furnaces are equipped with a modern solid emission capture system from the BMD GARANT company. This system ensures environmental responsibility and safety. The electric medium-frequency induction melting furnace INDUCTOTHERM ELPHIAC with a capacity of 2×5 tons serves as a backup melting device.
Gray cast iron
We specialize in the production of gray iron castings in quality from ČSN 42 2415 to ČSN 42 2425 (equivalent to EN-GJL-150 (GG 15) to EN-GJL-250 (GG 25)).
Ductile iron
We produce ductile iron in quality ČSN 42 23 05 (equivalent to EN-GJS-500-7 (GGG 50)).
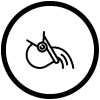
In the molding process, we excel at casting a wide range of weights from 2 kg to 100 kg into carefully made molds from synthetic bentonite mixtures. Our two automatic molding lines are equipped with molding machines from the renowned German company Heinrich Wagner Sinto. The frames (with a model device) are filled with molding mixture, the mold is blown with compressed air and then pressed. In addition, both lines offer the flexibility of inserting cores into the molds during the process, increasing the diversity and complexity of the castings.
HSP 3D frame molding line
One of our newest technologies is the HSP3D-2 line, which has been in operation since January 2023. This modern automatic line boasts of a split die plate and provides an impressive output of 60 complete molds per hour. The dimensions of the molding frame are 850 x 850 x 200/200 mm, which allows us to meet the diverse casting requirements with unmatched precision.
Half-form increase by up to 50 mm
The first generation of the HSP3D-1 molding line has been in operation since 2002, the size of the molding frame is 850 x 850 x 200/200 mm. It is possible to increase the half-form by 50 mm if needed. This line has a capacity of 50 complete molds per hour, which further increases our production capabilities and meets the requirements of various projects.
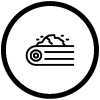
Our molding compound preparation process is a testament to modernity and efficiency. At the heart of this process is a mixing plant equipped with a modern MTI 2500 turbine mixer from TECHNICAL. To ensure accurate water dosing, we use an automated system from MICHENFELDER company, which guarantees the accuracy of our sand mixes. The molding mixture is cooled with air and, if necessary, cooled with water in the form of a water aerosol. What sets our molding compound process apart is its fully automated nature, which eliminates the need for human intervention and maximizes production efficiency while maintaining quality.
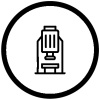
For core production, we use a LAEMPE LL20 machine, which boasts of a core mixture injection of a volume up to 30 liters, complemented by amine gas curing for exceptional core integrity. We also use the RÖPER 40 machine, which is known for its impressive core injection volume of up to 40 liters and the equally reliable amine gas curing process.
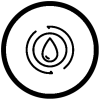
The main movement of castings from the molding lines to the tannery is ensured by a slow-moving link conveyor from the Magaldi company, which is followed by an efficient vibrating trough conveyor, which functions as a logistical connection between the stations. For easy handling, our specialized workers have CLANSMAN DYNAMICS hydraulic manipulator at their disposal, which makes the handling process more efficient.
We also cannot forget the cooling of castings in our cooling hall, where the castings are left to cool for up to 24 hours. After the cooling phase, the castings are carefully machined in the blasting machine. Here, all traces of molding material are precisely removed in order to achieve a perfect surface finish. Modern KONRAD RUMP blasting equipment with an impressive abrasive flow rate of 300 kg/min ensures that each casting is perfectly cleaned and ready for further processing. In addition, the device is equipped with a filter unit that ensures a clean and ecological process.
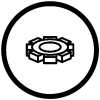
According to the customer’s requirements, we perform various surface treatments. Color variants in basic synthetic red-brown or black shades. We try to meet the diverse needs of customers, for example by comaxiting in different color shades or hot-dip galvanizing. We also offer machining of castings (turning, milling, drilling, etc.), both on conventional and NC and CNC machines.